A High Performance Wall for the 21st Century: 8″ External Woodfibre insulation with Long-screws
High Performance and Passive house design is based on both rigorous Building Science principles, but also inherited tradition. In this blog post we propose an alterative wall assembly based on first principles: high performance, low-cost, low embodied carbon, durable, efficient use of materials, and flexible.
But first, we will dive into the Building Science principles behind a wall and explain why the most common walls in Ontario are not so-much sound Building Science, as ‘inherited tradition’ . We’ll then explain our proposed 21st Century Wall (spoiler: using 8″ external insulation with long-screws to support the cladding, no insulation in the stud cavities, and a single air/water/vapour barrier on the outside of the sheathing, but on the warm side of the wall).
Building Science 101 – What makes a ‘good’ wall?
The walls of a building act as an environmental separator/moderator; keeping the outside and inside environmental conditions separate — all in order to keep the interior environment within the human comfort zone. The environmental conditions a wall must separate/moderate include rain, water vapor, wind, light, cold, and heat. These conditions are always combined together in varying proportions annually and diurnally.
Beyond simply separating/moderating the environment, Cooelarth believes a ‘good’ wall is also durable, low-carbon, and non-toxic.
Like the skin of our bodies or the cell wall, the walls in a building perform many functions, however in general these can be broken down into the following layers
– Rain Control
– Air Control
– Vapour Control
– Thermal Control
– Structural Support
– Finishing (inside and outside)
A good wall should be air-tight. From Building Science we learn that the best place for the air barrier is on the “warm” side of the wall, which prevent warm moist interior air from meeting cold dry exterior air, causing condensation (in the winter) and prevents the reverse in the summer.
A good wall should allow any vapour which enters the wall to escape and prevent vapour from entering unwanted areas. Issues can arise if multiple impermeable vapour control layers are included in the wall: these layers trap moisture (sandwich it) within the walls and thereby prevent the walls from drying out, causing mold and structural deterioration. This could happen if an impermeable house wrap is used on the exterior sheathing, and a impermeable vapour/air barrier, such as poly-vinyl, is used on the interior.
A ‘good’ wall has minimal thermal bridges. In Passive House design 8″ of continuous insulation is considered ‘thermal bridge free’. Issues which can arise when the thermal control layer is dis-continuous (i.e where there are thermal bridges). The danger with thermal bridges, other then increasing heating/cooling loads depending on the season, relates to building durability. In winter, thermal bridges can carry cool exterior temperature indoors and cause condensation on the interior, which can facilitate mold formation or degradation of the finishes and structure. In summer there can also be thermal bridges which can cause condensation for different reasons.
A ‘good’ wall minimizes the potential for water to be driven into the wall. This is why we always strive to use a ‘vented rainscreen’ approach and to provide multiple planes of protection for bulk water ingress. A vented rainscreen creates a zone behind the cladding which is the same pressure as the outside air, this means any wind-blown water is captured on the front face of the cladding, and is not driven into the wall assembly itself.
A ‘good’ wall is easy to build, has minimal layers, and minimizes the tradespeople and steps to assemble it.
There are many other attributes which make a ‘good’ wall, but we feel the above are some of the most important. In the short-space of this blog post we can’t get into the full Building Science of a wall, but suffice to say: a wall must deal with many, changing conditions, that can even work together to amplify or damped effects (i.e mositure can build-up in a wall over many years before it becomes a problem).
Inherited Tradition and Walls in Ontario
What we mean by ‘inherited tradition’ in the opening paragraph of this blog post is clearly exemplified in typical wood frame walls in Ontario.
In Ontario, over the last century, wood-frame walls were built with little to no insulation or air/vapour barriers. As time progressed in the 70’s and 80’s people started sealing the outside of the buildings with “housewrap”, filling the cavities between the wall studs with insulation, and placing a plastic vapour barrier on the warm inner-side of the walls, underneath the gypsum wall board. The typical wall studs were 2×4’s.
In 2016 the Ontario Building implemented minimum Energy Efficiency measures (via SB-12) which required continuous external insulation as well as set minimum insulation levels for the entire wall (among other things). To meet this requirements builders in Ontario started using 2×6 studs instead of 2×4’s (you can get R-22 in the 5.5″ of space within a 2×6 wall, compared to R-13 in a 2×4 wall), and also added 1.5-2″ of exterior insulation, typically foam or mineral wool.
As interest in Passive House design and an awareness of the important of highly insulated envelopes increased over the years, people have begun using a lot more insulation within the wall. We see the emergence of double-stud walls which are two sets of wood studs with a wider cavity in the middle which is then filled with insulation, as well as over 6″ of external insulation (with insulation also in the 2×4/2×6 stud cavities). From Coolearth’s point of view, these walls, while checking all the “boxes” of Building Science, often include many seperate layers of air, vapour, and rain membranes, multiple thermal control layers, and an uncessary amount of structural support (i.e in the case of double stud walls).
A further downside to many contemporary approaches to high performance walls in Ontario is that the structure (wood studs) is not kept at room temperature. What we mean by this is that whatever the indoor and outdoor temperatures are, there is always a thermal gradient within the wall which connects the two temperatures. Depending on where the thermal and structural layers are placed within the wall, the structural layer might be colder or warmer then the interior temperature — this can open up the risks of degradation or mold formation on the structural elements.
Therefore, let us introduce, what we might call a wall for the 21st centry!
A High Performance Wall for the 21st Century: 8″ External Woodfibre insulation with Long-screws
After much research and synthesis we present to you a wall system for Ontario that is high performance, low-cost, simple to build, durable, and long lasting.
We created a 1:1 prototype of the wall to illustrate the concept:
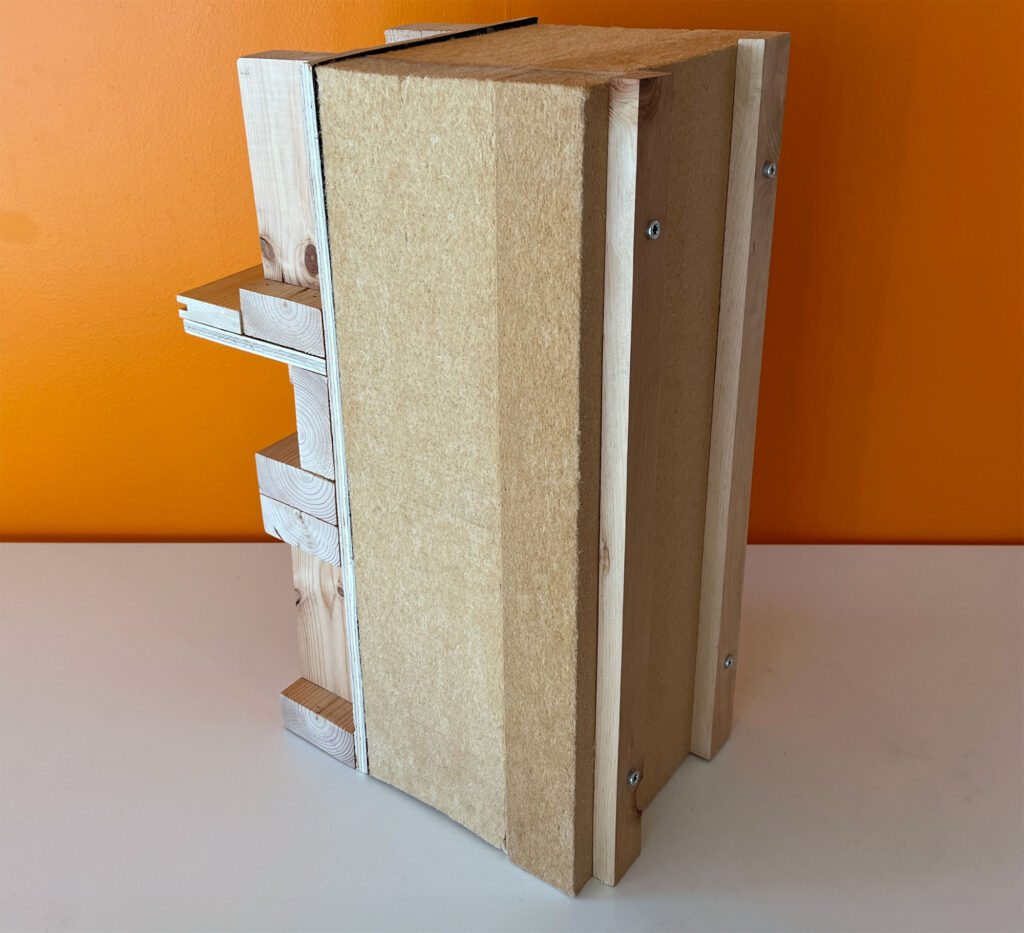
The wall is composed of (from interior to exterior):
– 2×4 studs @ 16″ spacing (or 2×6 at 24″ spacing).
– 5/8″ Exterior Grade Plywood (for durability, longevity, low-toxicity).
– Vapour and Air and Water Impermeable Membrane. There is only one membrane in the whole wall! (in our prototype it is Blueskin SA).
– 8″ of Continuous wood-fibre insulation (in the case of the 1:1 model prototype we created it is composed of 4.5″ of STEICO ThermDry and 2.5″ of STEICO UniversalDry insulation). In our view as architects, this insulation is both dense and water-repellant and thus acts as a secondary plane of protection, however some municipalities interpret the Ontario Building Code as requiring a further ‘Secondary Plane of Protection’ in which case a vapour permeable house wrap (stapled, not taped) such as Tyvek would be sufficient and cost-effective to address ther concerns.
– Steel long-screws with wood strapping (in our prototype it is Rothoblaas DGZ).
– A 3/4″ vented cavity (as narrow as possible to minimize risk of forming fire in the cavity — although this is dependent on the required strapping dimensions).
– Lightweight cladding of choice (metal, wood, fibrecement).
You can see the interior view of the wall below. We haven’t shown it with drywall. Some clients opt to use this wall with the wood framing exposed and painted white. Others elect to use the traditional gypsum wall board (drywall). Other opt for wood boards, or plaster.
You can see that the structure of the home (floor, walls, and roof) is all within the thermal, air, and vapour control layers — the structure is kept room temperature at all times. Any vapour which builds up within the interior or exterior of the wall can dry. The thermal control layer is 8″ of insulation with the only thermal bridges being the long-screws.
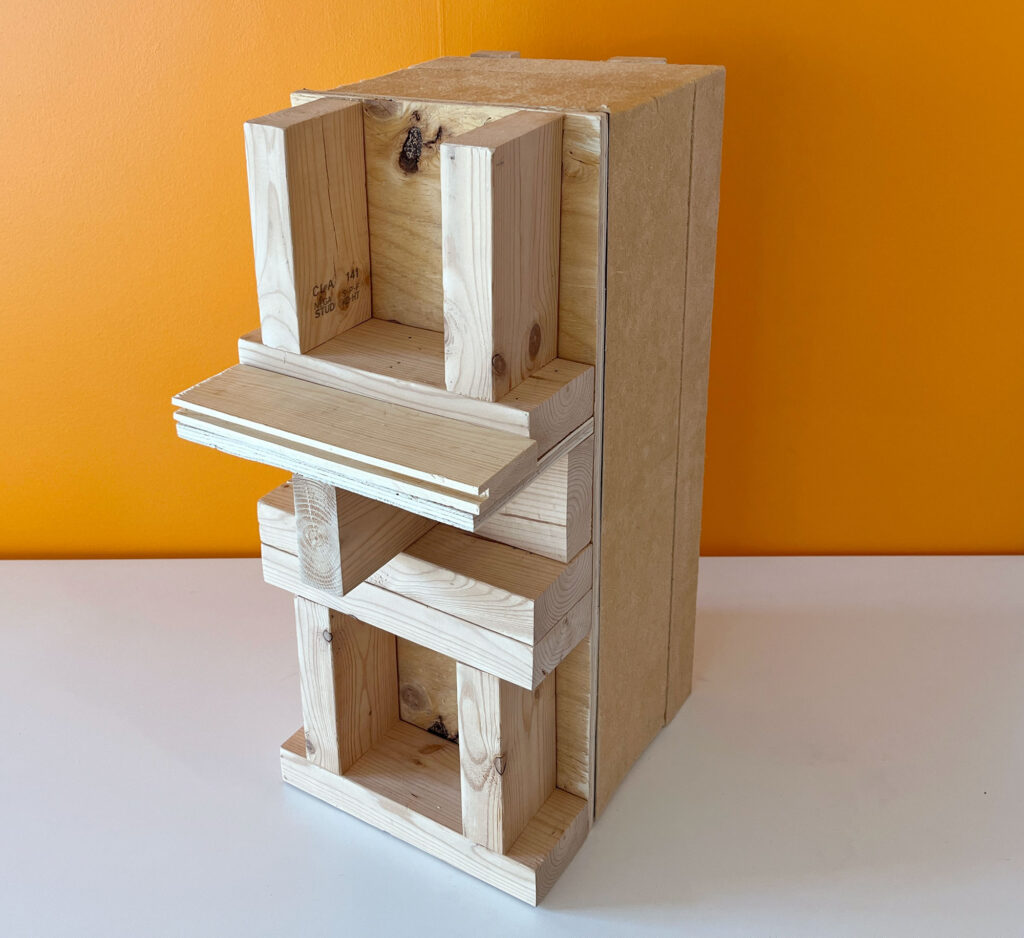
Below is a photo of the DGZ long-screw from Rothoblaas, and the two layers of STEICO woodfibre insulation. This same wall wood also work with the rigid mineral wool insulation (such as Rockwool Comfortboard). You can see the Blueskin SA air/water/vapour membrane, and the 2×4 studs.
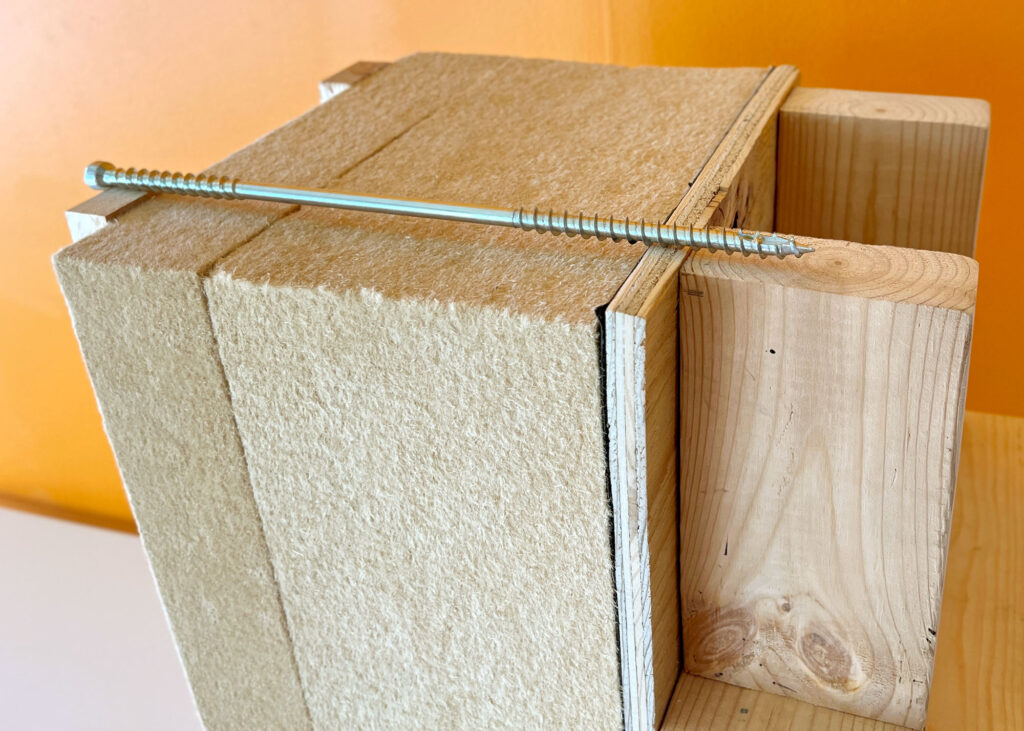
Now, woodfibre insulation is not that common in North America at the moment, but it seems to us that there is a lot of potential for it to become commonplace.
What is woodfibre and what are its benefits?
“Woodfibre insulation is a safe, natural, and high performing insulation alternative to other common synthetic insulation options.”
- Woodfibre boards are typically made from waste woodfibre that is collected from sawmill factories, which is then heated and pressurized to form modular boards.
- The thermal insulation and storage properties of the boards are ideal for use in a wide range of construction, including as continuous external insulation
- Other benefits of using wood fibre insulation include:
- Low-toxicity
- Embodies carbon
- Good thermal insulation
- Fire resistance – a char layer forms on the outside protecting the inside. Vapour permeability